Unlocking the Power of Welding WPS: Strategies for Performance and Security in Fabrication
In the world of construction, Welding Procedure Requirements (WPS) stand as the foundation of welding operations, determining the required actions for accomplishing both efficiency and safety and security in the construction process. Recognizing the ins and outs of WPS is paramount to using its full possibility, yet lots of organizations have a hard time to unlock truth power that lies within these records (welding WPS). By delving right into the techniques that maximize welding WPS, a world of boosted productivity and enhanced safety waits for those ready to explore the subtleties of this vital aspect of fabrication

Value of Welding WPS
The relevance of Welding Procedure Requirements (WPS) in the fabrication market can not be overemphasized. WPS act as an important roadmap that describes the needed actions to make sure welds are performed regularly and appropriately. By specifying important specifications such as welding procedures, products, joint designs, preheat temperatures, interpass temperature levels, filler steels, and post-weld warmth therapy needs, WPS provide a standard approach to welding that enhances effectiveness, high quality, and safety and security in manufacture procedures.
Adherence to WPS helps in achieving uniformity in weld top quality, lowering the likelihood of defects or structural failures. This standardization also helps with compliance with market guidelines and codes, making sure that produced structures meet the required security requirements. Furthermore, WPS paperwork allows welders to duplicate successful welding procedures, resulting in consistent results across various tasks.
Essentially, the thorough growth and rigorous adherence to Welding Treatment Specs are critical for supporting the integrity of welded frameworks, safeguarding against prospective risks, and supporting the track record of fabrication business for delivering high-quality services and products.
Crucial Element of Welding WPS
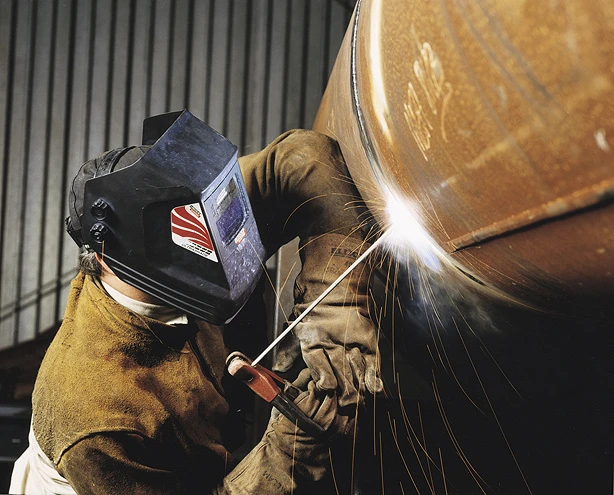
Enhancing Performance With WPS
When enhancing welding procedures, leveraging the crucial elements detailed in Welding Procedure Specs (WPS) becomes crucial for improving procedures and taking full advantage of efficiency. One way to improve effectiveness with WPS is by meticulously picking the appropriate welding criteria. By sticking to the specific guidelines offered in the WPS, welders can make sure that the welding tools is set up properly, bring about consistent and top notch welds. In addition, following the pre-approved welding sequences outlined in the WPS can dramatically reduce the time invested on each weld, inevitably increasing overall efficiency.
Moreover, correct training and accreditation of welders in understanding and implementing WPS can better improve effectiveness. Ensuring that all staff member are well-versed in interpreting and performing the WPS accurately can decrease mistakes and rework, conserving both time and resources. Frequently reviewing and upgrading the WPS to integrate any kind of lessons found out or technical improvements can likewise add to efficiency renovations in welding procedures. By accepting the guidelines stated in the WPS and constantly seeking ways to important link maximize procedures, fabricators can achieve greater effectiveness levels and superior outcome.
Ensuring Safety in Manufacture

Making certain safety in manufacture involves a multifaceted strategy that incorporates various elements of the welding process. Welders should be furnished with proper equipment such as helmets, handwear covers, and safety clothes to minimize risks associated with welding tasks.
Furthermore, adherence to correct air flow and fume extraction systems is important in maintaining a healthy and balanced workplace. Welding fumes have damaging substances that, if breathed in, can position significant health dangers. Applying effective ventilation procedures helps to decrease exposure to these unsafe fumes, promoting respiratory health among workers.
Routine tools upkeep and examinations are also vital for ensuring security in fabrication. Malfunctioning equipment can result in crashes and injuries, highlighting the value of regular checks and prompt fixings. By focusing on safety procedures and cultivating a culture of understanding, construction facilities can develop a safe and secure and effective job atmosphere for their personnel.
Carrying Out WPS Best Practices
To improve operational performance and make certain quality results in manufacture processes, incorporating Welding Treatment Requirements (WPS) finest practices is extremely important. Choosing the appropriate welding procedure, filler material, and preheat temperature level specified in the WPS is vital for achieving the desired weld high quality. Making sure that certified welders with the essential certifications carry out the welding procedures according to the WPS guidelines is vital for consistency and dependability.
Final Thought
In verdict, welding WPS plays an important duty in guaranteeing performance and safety in construction procedures. By focusing on crucial elements, improving performance, and implementing finest techniques, companies can enhance their welding procedures. It is essential to prioritize precaution to stop crashes and ensure a smooth production procedure. By adhering to these methods, services can open the complete capacity of welding WPS in their fabrication operations.
In the world of fabrication, Welding Procedure Specifications (WPS) stand as the look at this site backbone of welding operations, dictating the required steps for achieving both performance and security in the fabrication procedure. By defining vital specifications such as welding procedures, materials, joint styles, preheat temperatures, interpass temperature levels, filler metals, and post-weld warm treatment demands, WPS provide a standardized approach to welding that enhances performance, top quality, and safety and security in manufacture procedures.
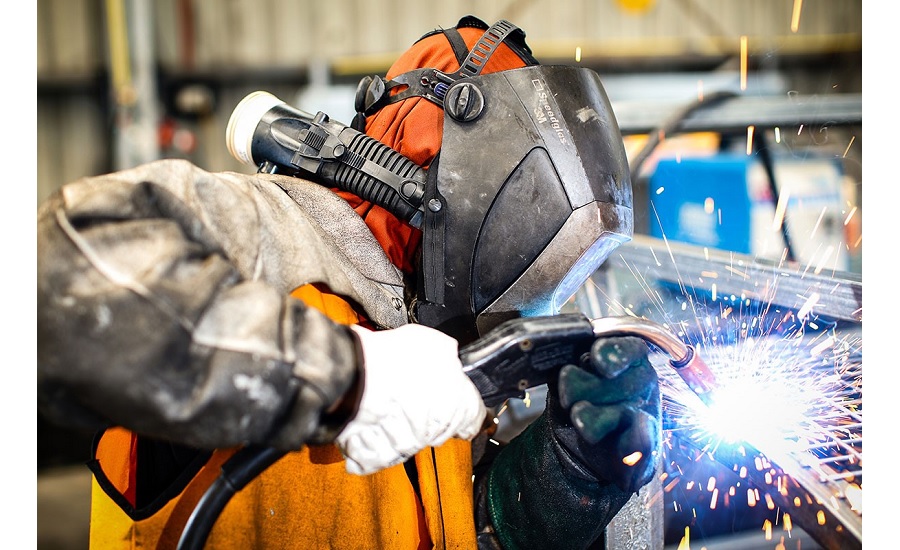
When optimizing welding operations, leveraging the vital aspects described in Welding Procedure Requirements (WPS) comes to be necessary for enhancing procedures and taking full advantage of efficiency. (welding WPS)
Comments on “Understanding Welding WPS: Comprehensive Overview for Welders”